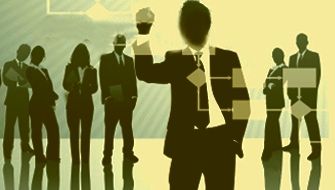
HELIOS QUALITY SYSTEMS - BACKGROUND
Helios was created because the regulatory and compliance load upon a range of businesses is growing.
Many requirements such as ISO Standards are entered into voluntarily, or because customers demand these approvals, others because the industry sector mandates specific levels compliance both as a means of assuring quality, security and safety, but also to create a barrier to entry and thus minimise the competition.
Helios have experience of Quality / Compliance management within World Leaders in the following industries:
- Aerospace
- Military
- Printed Circuit
- Civil - Construction
- Electronics
- Electro-Mechanical
- Automotive
- Secure Banking
Helios can help to ensure that your business stays current, follows the rules, passes the audits, and realises the benefits of the industry applicable schemes whilst minimising additional paperwork and red-tape.
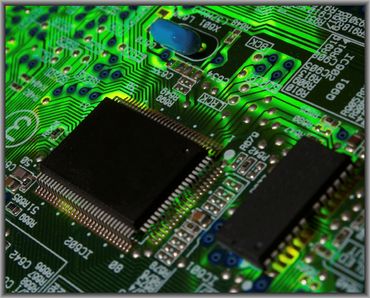
THE COST OF QUALITY
The cost of quality is the accumulated cost of not creating a quality product. These costs can include reworking a product, testing it, field service to make corrections after a product has been installed, and replacing a faulty product. This aggregate cost is reported to management to give them a basis for ensuring that processes always produce to customer expectations
A customer perceives a product as having a high level of quality if it conforms to his expectations. Thus, high quality is really just making sure that a product does what a customer expects it to do.
This view of quality means that a company can eliminate any costs that customers have no quality perceptions about. The cost reduction can impact a great many areas. For example, it may be perfectly acceptable to use lower-quality or thinner materials, or to allow blemishes in areas where customers cannot see them, or to allow production at a lower tolerance level than is currently the case (which eliminates some rework costs).
There are two types of quality that a company should be concerned about, one of which originates in the engineering department, while the other is the responsibility of the entire organization. They are:
- Quality of design. This is the ability of a company to design a product that conforms to the quality expectations of a customer. In other words, the quality that customers expect is designed into the product. This type of quality requires a considerable amount of interpretation of what engineers think customers want, and how these wishes are integrated into the final product design. If quality is not designed into the basic structure of a product, there is no way to improve the quality situation later, short of replacing the product with a new version.
- Quality of conformance. This is the ability of a company to produce a product that conforms to the original product design. This type of quality is not just the responsibility of the production department; the purchasing staff has to acquire the correct materials, the shipping department must deliver it without damage, and the marketing department must communicate the attributes of the product that matter most to customers.
There are several types of costs that are impacted by the quality of a product. They are:
- Prevention costs. These are costs incurred to avoid product failures. These costs include production procedure development, staff training, product testing, preventive maintenance on the machinery used to create products, and supplier qualification assessments.
- Appraisal costs. These are the costs of inspection needed to reduce the risk of sending defective products to customers. These costs include supplier component testing, quality control product testing, process analysis, and the cost of any testing equipment.
- Internal failure costs. These are the costs associated with defective products that are uncovered prior to delivery to customers. These costs include rework of the defective products, additional testing of the reworked products, scrap, purchasing replacement parts, and the lost profit on products that must be sold as seconds.
- External failure costs. These are the costs associated with defective products that are uncovered subsequent to delivery to customers. These costs include lost revenue from customers who will not buy from the company again, the processing of returned goods, administering warranty claims, field service costs, liability lawsuits, and possibly even a comprehensive product recall.
It is more cost-effective to pay for cost improvements in-house, rather than waiting for customers to discover defects. The primary reason is that customers are much less likely to buy from the company again if they discover defects, which can make external failure costs more expensive than all of the other costs combined.
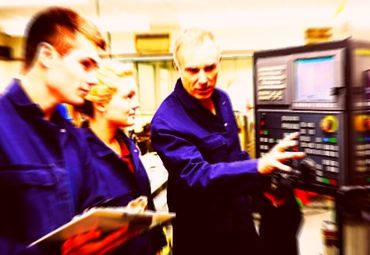
TRAINING
Helios are able to design, develop and deploy training courses which can support your staffs understanding of their processes, and their place within the business.
Quality and Compliance awareness courses can be tailored for your industry sector and prove invaluable in ensuring buy-in from staff when regulations drive organisational change
Helios Quality Systems can provide mentoring of internal quality / audit staff to ensure that the business is able to continue its improvement journey and stay compliant.